1. Industrial Wood: What Is It?
Industrial wood stands out from natural wood through a variety of made wood panels. These panels come from wood chips stuck together with top-notch glues or safe chemicals. This method keeps the wood’s quality intact and results in tough long-lasting wood pieces.
Known worldwide for its role in Wood-Based Panels industrial wood puts to good use leftover wood from making furniture recycled wood, and even tree branches and tops. This clever approach aims to cut down on waste from regular wood use and helps fight illegal logging that hurts the environment.
Industrial wood is available in many types and sizesIndustrial wood has two main parts: the inside and the outside. The inside gives strength to the wood. Manufacturers use molds to make boards like MDF, MFC, and HDF for this part. The outside has two jobs: it makes the wood look good and protects the wood parts. By putting these two parts together industrial wood products last a long time, stay strong, and look nice.
2. What Are the Types of Industrial Wood Cores?
Selection of the proper industrial wood core is a very important issue. In the perspective of sustaining longevity and strength in the product, its importance also lies in the safety of the user. There are many types of industrial wood cores available, each having a different characteristic. Therefore, selection should be done with care. This is not about reaching for any old core, but rather, you have to put your mind into it in order to do the best.
When choosing MFC, you get a super strong and water-resistant board. MDF is great for painting and blocking noise. HDF is tough as nails and keeps water out like a champ. Industrial Plywood stays flat and doesn’t warp . Each type of board has its own job in making wood stuff work better and look cooler. First, to make sure you end up with something awesome, you gotta give some thought to what you need the wood for. Then, pick the right core, and you will have a product far superior to that which you expect. It shall work great and please people when used.
2.1 Melamine Faced Chipboard (MFC)
MFC Timber is lumber which consists of small sections of trunks, branches, or twigs of the Poplar, Eucalyptus, and rubber tree. These trees are grown on purpose and are known to be super strong, have a big surface area, and help keep nature diverse. To make MFC wood, people chip these materials, mix them with special glues, and squish them into boards. These boards are available in other thicknesses that are, 9mm, 12mm, 15mm, 18mm, 25mm among others. You can find different types of MFC boards too. There’s the white core, the green core that doesn’t get messed up by water , and the black core. Each type has its own special use.
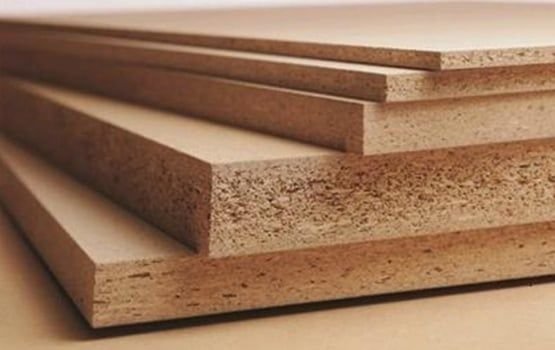
The middle part of the particle board however is rough as it has visible wood shavings. One such core is used in making many items, such as tables and wardrobes.
2.2 Medium Density Fiberboard (MDF) Core
Medium Density Fiberboard (MDF) Process MDF includes tree limbs reduced to powder and mixes adhesives to make different thicknesses of the boards. MDF boards are preferred by most people due to their tendency to allow easy bonding of paint and veneers to their surfaces. This makes them ideal for furniture in vibrant designs like a children’s room or a showroom where lots of colors are desired. MDF also possesses sound insulation capabilities and is also efficient in temperature retention in an enclosed space.

2.3 High Density Fiberboard (HDF)
HDF or High Density Fiberboard- a much denser and heavier kind of artificial wood board. To begin with, the production process of HDF begins with the collection of wood dust from the residues of wood products manufacturing. In a sophisticated plant, the wood powder is treated with some agents that would strengthen the wood and also protect it from insects. They also dry it out. Then, they squish it really hard (like 850-870 kg/cm²) to make HDF boards that are 2,000mm x 2,400mm big. These boards can be anywhere from 6mm to 24mm thick, depending on what you need. This whole process makes sure HDF is top-notch and quick to make so it’s great for lots of different things in the wood industry.
HDF is a top pick for industrial wood stuff because it keeps water out and is hard. It’s good at blocking sound and keeping heat in so people use it for lots of things. The inside part is made super using wood frames that are dried in big ovens and treated so they don’t get all bent out of shape or puffy. You can also make HDF look how you want with about 40 different paint colors to pick from so it fits in with all sorts of designs. HDF is tough, works well, and looks nice, which is why a lot of people in the industrial wood business like to use it.
2.4 Industrial Plywood
Industrial plywood is made by sticking thin wood sheets together. This keeps it strong and stops it from bending out of shape. The middle layer helps keep everything in place. Plywood looks good and works well in furniture. It lasts a long time, which is why many people pick it for industrial wood stuff that needs to last.
2.5 Particle Board (PB)
The particle board is made up of wooden materials from various species of trees grown in the forest like rubberwood or poplar and is carefully processed to make strong boards. Coated with melamine or acrylic, it offers a wide array of colors and is recognized for its cost-effectiveness and consistent hardness, albeit with a slightly lower load-bearing capacity compared to other materials.

3. Popular Wood Grain Surface Types Nowadays
For that matter, special coats or thin layers are laid atop most industrial wood to enhance the look and increase its durability. Most of the apparent timber surfaces you find in furniture today are melamine-faced chipboard, laminates, veneers, and super glossy finishes. Each of these has its own neat features that give industrial wood products a great look and make them work well. These coatings help to boost how the wood appears and how it stands up to wear and tear over time.
People like MFC a lot because it comes in many colors, looks bright and uniform, and doesn’t bend or attract insects. Laminate surfaces have a thicker fake resin layer to make them more durable. You can spot the difference between melamine and laminate by their thickness. Veneer finishes put actual wood on top to give things a fancy and natural look. They showcase the wood’s rich appearance and texture. High gloss finishes have a smooth and fresh look. They reflect light and make things appear shiny and polished.
Companies can make industrial wood items fit certain styles and work better by picking the right surface coverings or finishes. These surface treatments don’t just make the furniture prettier – they also help it last longer and do its job better. This makes them super important when making top-notch industrial wood stuff. To make it look more natural, people who make these things can customize products to meet specific design likes and performance needs by choosing the right surface veneers or coatings. The treatments given affect the appearance and durability of the furniture, hence these are helpful in the production of quality industrial timber.
3.1 Melamine Faced Chipboard (MFC)
The purpose of the melamine surface is to provide a thin application of synthetic resin ranging between 0.4 to one millimeter plastered over surfaces. It is often used for strengthening chipboard and/mid density fiberboard materials. After they put the melamine on, the boards usually come in 18mm and 25mm thicknesses. This makes them good for lots of industrial wood projects. Melamine-faced chipboard (MFC) often comes in sizes like 1220 x 2440 mm or 1830 x 2440 mm, which gives people more options when they’re designing and building stuff.
MFC is available in over a hundred colors that are quite bright and even. It can be applied to offices, homes, and hotels. It is long-wearing, cannot easily get out of shape and neither can bug infestations, hence its look lasts for quite a long period. Given its many colors and resistant qualities, MFC is ideal for decorative purposes in a structured area.
But remember, MFC has a weak spot – it doesn’t handle moisture and water well. This means you’ve got to think about where you’re using it and how much humidity it might face. Even with this drawback, MFC is still a hit in the wood industry. What’s the reason? There are many reasons: vibrant tones, robustness, appealing design. This is likely the reason why individuals continue to produce items out of it aesthetically pleasing and very sturdy.

3.2 Laminate Surface
Laminate surface has a synthetic resin layer, which is thicker between 0.5 and 1mm. People put it on chipboards, MDF, and other similar stuff. You can bend it using post-forming technology. The regular thickness for Fami Laminate surface is 0.75 mm. Some call it Melamine HPL, too.
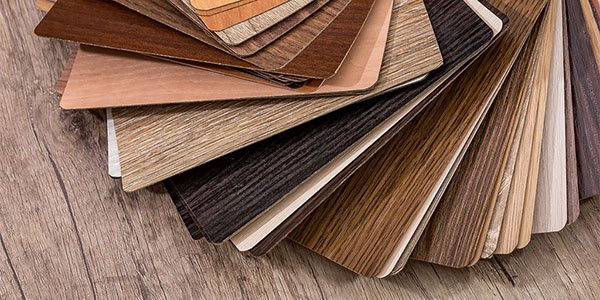
3.3 Veneer Surface
Veneer is a fantastic option for adding a touch of natural beauty to industrial wood products. It consists of thin sheets of recycled natural wood, which vary in thickness between 0.3 and 0.6 mm. It is easy to manipulate these veneer sheets. They are much cheaper than solid wood and can be molded into desired curves. Thus, various types of products with impressive wood veneers are available in various patterns and colors because of the veneer outer layer used for decoration.

3.4 Vinyl Surface
The vinyl surface is available in standard thickness options of 0.12mm, 0.18mm, and 0.2mm and has a distinctive configuration consisting of PVC and a Korean import coating layer. Looking at this picture we can assume that this new innovative vinyl surface is often used in association with laminates for producing wood based products giving an all rounded hardness.
4. Conclusion
Nowadays, the wood industry has enormous development opportunities that were brought about by both the market’s increasing demand and growing concern for environmental protection. Besides, the wood sector needs to be flexible and sensitive towards the requirements of sustainable forest management, as well as competitive in manufacturing technologies.
Are you looking to provide your customers with exquisite industrial wood? With a wealth of experience, HPC is able to provide a wide range of high-standard products. Contact us today for more information and discover the perfect pieces for your customers!